Metal Jacketed Gasket, as the name suggests, consist of a metallic outer shell with either a metallic or non-metallic compressed fiber filler. The filler material gives the gasket resilience, while the metal jacket protects the filler and resists pressures, temperatures and corrosion.
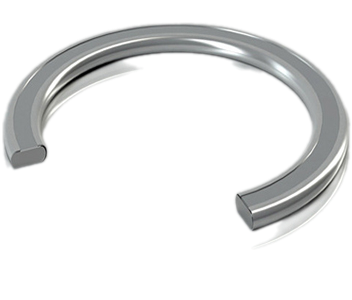
TYPE |
CODE |
Single Jacketed Gasket |
LSJ |
Double Jacketed Gasket |
LDJ |
Double Jacketed Corrugated Gasket |
LDJC |
Double Jacketed Double Shell Gasket |
LDJDS |
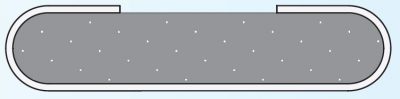 |
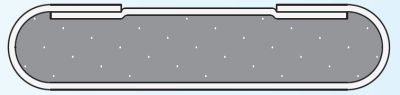 |
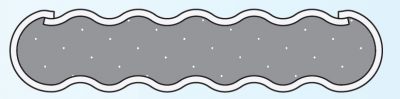 |
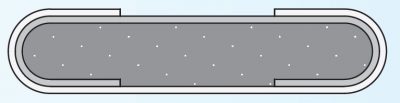 |
LeGiaSeal Single Jacketed Gaskets are used in air tool applications and engine applications where space is limited, gasket seating surfaces are narrow and relatively low compressive forces are available for seating the gasket. |
LeGiaSeal Double Jacketed Gaskets are probably the most commonly used style of gaskets in heat exchanger applications. They are also extensively used in standard flanges. Since most double jacketed gaskets are custom made, there is virtually no limit to size, shape or configuration. |
LeGiaSeal Double Jacketed Corrugated Gaskets are an improvement on a plain-jacketed gasket. The corrugations on the gasket will provide an additional labyrinth seal. Enhancing its compressive characteristics. Main sealing performance of double jacketed corrugated gasket still relies on the inner lap. |
LeGiaSeal Double-Jacketed Double-Shelled Gaskets are similar to the double jacketed gasket. But it uses two shells in the fabrication of the gasket instead of using a shell and a liner. It has the advantage of a double lap at both the ID and the OD of the gasket, adding greater stability to the gasket. The construction will withstand higher compressive loads. Double-shell gaskets are normally restricted to use in high pressure applications. |
JACKET MATERIALS
Material |
Temperature (ºC) |
Carbon Steel |
540ºC |
304 |
760ºC |
316 |
760ºC |
31803 |
300ºC |
321 |
760ºC |
Hastelloy C-276 |
1090ºC |
Monel 400 |
820ºC |
347 |
870ºC |
Alloy 20 |
870ºC |
N06625 |
1290ºC |
N08800 |
1290ºC |
Inconel 600 |
1290ºC |
410 |
760ºC |
Titan Gr.1 |
1090ºC |
FILLER MATERIALS
Material |
Temperature (ºC) |
Graphite |
-212 to +500ºC |
PTFE |
-120 to +450ºC |
Ceramic |
-212 to +1100ºC |
Non-Asbestos |
-120 to +450ºC |
NOTE:
Filler Thickness: The filler thickness shall be a minium of 0.38mm
Jacket Thickness: The jacket metal thickness shall be a minium of 1.5mm
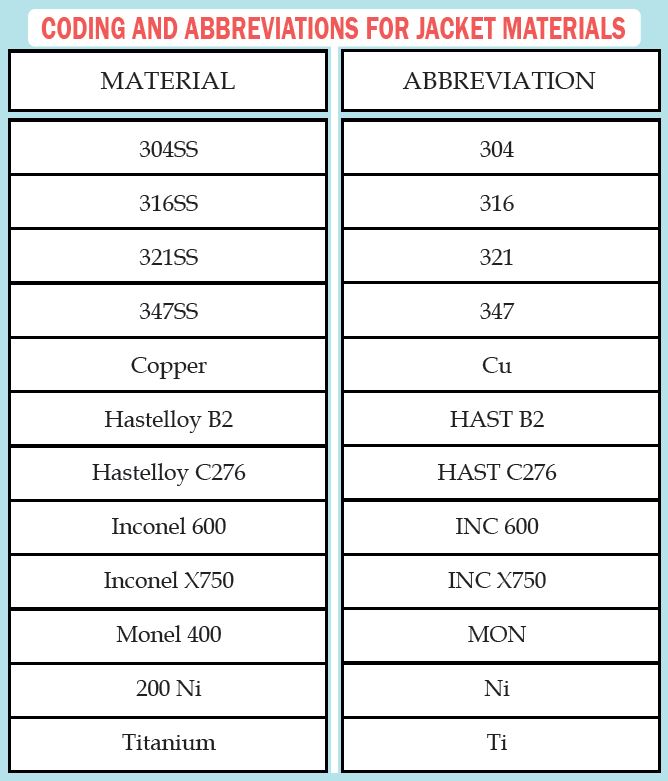
FEATURES
Suitable for narrow flanges, good blow-out resistance. The metal jacket covering the filler material prevents contamination, suitable for high temperatures, ensures high elasticity and recovery. Nearly any dimension and shape can be mode, economical &.perfect sealing stability, easy to handle and install.
CLASSICAL APPLICATIONS
Sealing of heat exchangers |
Pipe flanges |
Boilers and process equipment |
Valve Bonnet Gasket |
Autoclaves |
High pressure oil field drilling and production equipment |
Pressure vessels |
Gas and chemical plants |
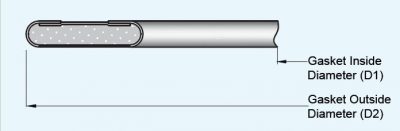
Flange Size (NPS) |
Gasket Inside Diameter (D1) [Note (1)] |
Gasket Outside Diameter (D2) by Pressure Class [Note (1)] |
150# |
300# |
400# |
600# |
900# |
1500# |
2500# |
1/2″ |
22.4 |
44.5 |
50.8 |
[Note (2)] |
50.8 |
[Note (2)] |
60.5 |
66.8 |
3/4″ |
28.7 |
54.1 |
63.5 |
[Note (2)] |
63.5 |
[Note (2)] |
66.8 |
73.2 |
1″ |
38.1 |
63.5 |
69.9 |
[Note (2)] |
69.9 |
[Note (2)] |
76.2 |
82.6 |
1 1/4″ |
47.8 |
73.2 |
79.5 |
[Note (2)] |
79.5 |
[Note (2)] |
85.9 |
101.6 |
1 1/2″ |
54.1 |
82.6 |
92.2 |
[Note (2)] |
92.2 |
[Note (2)] |
95.3 |
114.3 |
2″ |
73.2 |
101.6 |
108.0 |
[Note (2)] |
108.0 |
[Note (2)] |
139.7 |
143.0 |
2 1/2″ |
85.9 |
120.7 |
127.0 |
[Note (2)] |
127.0 |
[Note (2)] |
162.1 |
165.1 |
3″ |
108.0 |
133.4 |
146.1 |
[Note (2)] |
146.1 |
165.1 |
171.5 |
193.8 |
4″ |
131.8 |
171.5 |
177.8 |
174.8 |
190.5 |
203.2 |
206.5 |
231.9 |
5″ |
152.4 |
193.8 |
212.9 |
209.6 |
238.3 |
244.6 |
251.0 |
276.4 |
6″ |
190.5 |
219.2 |
247.7 |
244.6 |
263.7 |
285.8 |
279.4 |
314.5 |
8″ |
238.3 |
276.4 |
304.8 |
301.8 |
317.5 |
355.6 |
349.3 |
384.3 |
10″ |
285.8 |
336.6 |
358.9 |
355.6 |
397.0 |
431.8 |
431.8 |
473.2 |
12″ |
342.9 |
406.4 |
419.1 |
416.1 |
454.2 |
495.3 |
517.7 |
546.1 |
14″ |
374.7 |
447.8 |
482.6 |
479.6 |
489.0 |
517.7 |
574.8 |
[Note (2)] |
16″ |
425.5 |
511.3 |
536.7 |
533.4 |
562.1 |
571.5 |
638.3 |
[Note (2)] |
18″ |
489.0 |
546.1 |
593.9 |
590.6 |
609.6 |
635.0 |
701.8 |
[Note (2)] |
20″ |
533.4 |
603.3 |
651.0 |
644.7 |
679.5 |
695.5 |
752.6 |
[Note (2)] |
24″ |
641.4 |
714.5 |
771.7 |
765.3 |
787.4 |
835.2 |
898.7 |
[Note (2)] |
Flange Size (NPS) |
Gasket Inside Diameter (D1) [Note (1)] |
Gasket Outside Diameter (D2) by Pressure Class [Note (1)] |
150# |
300# |
400# |
600# |
900# |
26 |
673.1 |
771.7 |
831.9 |
828.8 |
863.6 |
879.6 |
28 |
723.9 |
828.8 |
895.4 |
889.0 |
911.4 |
943.1 |
30 |
774.7 |
879.6 |
949.5 |
943.1 |
968.5 |
1006.6 |
32 |
825.5 |
936.8 |
1003.3 |
1000.3 |
1019.3 |
1070.1 |
34 |
876.3 |
987.6 |
1054.1 |
1051.1 |
1070.1 |
1133.6 |
36 |
927.1 |
1044.7 |
1114.6 |
1114.6 |
1127.3 |
1197.1 |
38 |
977.9 |
1108.2 |
1051.1 |
1070.1 |
1101.9 |
1197.1 |
40 |
1028.7 |
1159.0 |
1111.3 |
1124.0 |
1152.7 |
1247.9 |
42 |
1079.5 |
1216.2 |
1162.1 |
1174.8 |
1216.2 |
1298.7 |
44 |
1130.3 |
1273.3 |
1216.2 |
1228.9 |
1267.0 |
1365.3 |
46 |
1181.1 |
1324.1 |
1270.0 |
1286.0 |
1324.1 |
1432.1 |
48 |
1231.9 |
1381.3 |
1320.8 |
1343.2 |
1387.6 |
1482.9 |
50 |
1282.7 |
1432.1 |
1374.9 |
1400.3 |
1444.8 |
[Note (2)] |
52 |
1333.5 |
1489.2 |
1425.7 |
1451.1 |
1495.6 |
[Note (2)] |
54 |
1384.3 |
1546.4 |
1489.2 |
1514.6 |
1552.7 |
[Note (2)] |
56 |
1435.1 |
1603.5 |
1540.0 |
1565.4 |
1603.5 |
[Note (2)] |
58 |
1485.9 |
1660.7 |
1590.8 |
1616.2 |
1660.7 |
[Note (2)] |
60 |
1536.7 |
1711.5 |
1641.6 |
1679.7 |
1730.5 |
[Note (2)] |
Schedule of Standard Shapes For Heat Exchanger Gaskets. Other bar configurations available on request
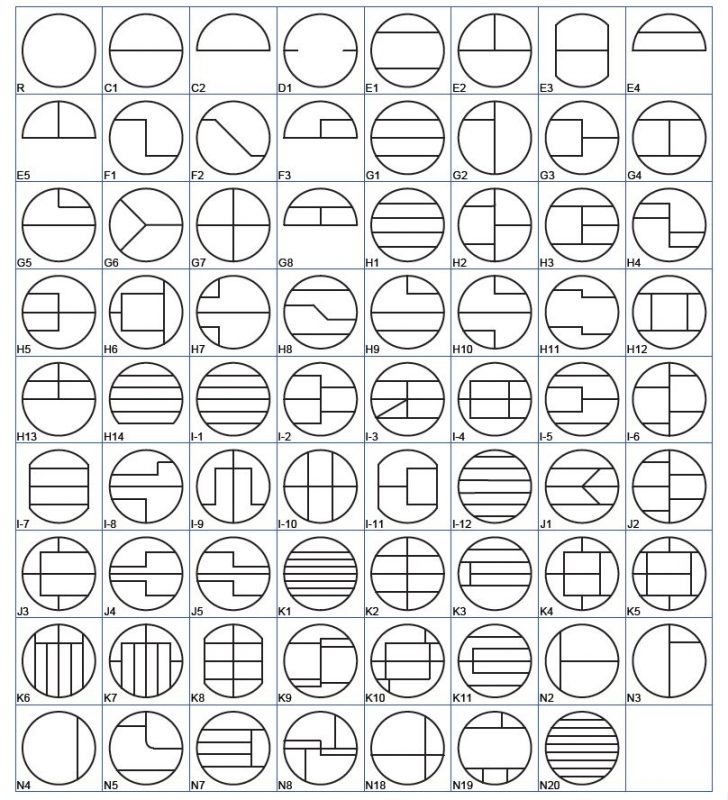